Drying units spray type are used in the chemical industry to produce high quality final products. The dried material is obtained in the form of a fine free-flowing powder which is easily transported, packed and has an attractive presentation. In dryers spray-type a high rate of evaporation of moisture is achieved due to dispersed material distribution in the working chamber, through which the heated air or flue gases moves, while the specific surface of evaporation becomes so large that the drying process is completed very quickly (approximately 15 - 30 seconds). Thus devices of the spray type can achieve quick-drying in sparing conditions of temperature, followed by obtaining high-quality, well-soluble product which does not require further grinding.
Application:Chemical industry: alkali metal fluorides, formaldehyde silicic acid, catalysts, sulfuric acid, amino acids, fertilizer, etc.
Manufacture of plastics and resins: AB, ABS plastics, resin of uric acid, phenol aldehyde resin, urea-formaldehyde resins, formaldehyde resins, polyethylene, polychloroprene, etc.
Food industry: cereal powders, chicken meat powder, seasoning meat, milk powder and its substitutes, cocoa, instant tea and coffee,
soy and peanut protein, protein hydrolysate, substitute of egg white (egg yolk), sugar from corn extract, corn starch, glucose, pectin, malt, ascorbic acid, etc.
Manufacture of ceramics: aluminum oxide, magnesium oxide, material for the manufacture of ceramic tiles, talc, etc.
Technological scheme of drying with the spraying:
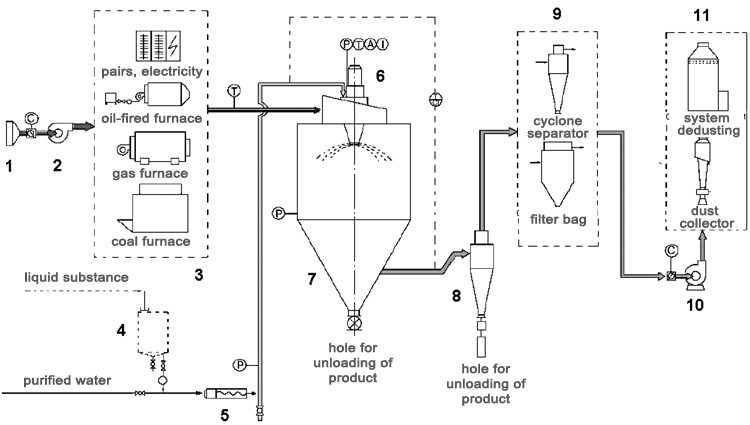
1. Filter; 2. Ventilator; 3. Heater; 4. Container with feedstock (or fitter of feedstock supply); 5. Injection pump; 6. Atomizer;
7. Drying chamber; 8. 1st dust-recovery circuit; 9. 2nd dust-recovery circuit; 10. Ventilator; 11. 3rd wet dust-recovery circuit.
Operating principle:
The drying process begins with the spraying of the liquid feedstock into the drying chamber. Feed is carried out by means of a centrifugal spray or atomizers. When drops are contacted with a stream of hot air, they are converted into a powder. Speed of the process of evaporation of moisture can be controlled by changing the size of a stream of hot air. Finished products are withdrawn from the bottom of the unit continuously; the powder has a high quality, high purity, uniform homogeneous structure and good solubility. After the drying process, air is removed from the system by exhaust fan.
There are following movement pattern circuits of the coolant and suspension in spray dryers in industrial environments: co-current and counter-current. In case of co-current flow movement of the drying agent and suspension feeding of suspension is produced on top of the drying tower using atomizers or a centrifugal spray. In the case of feeding the starting material from the bottom of the drying tower (using a spray atomizer under high pressure) circuit of counter-current unit operation is performed. In both cases preheated drying agent is fed from the top of the tower through the air distribution device.
Particularly preferred is the co-current, because such mode allows drying at high temperatures avoiding overheating of the material and the rate of deposition of particles is composed of speed of their soaring and the speed of the drying agent. Velocity of a gas in the chamber, counting its total cross section, generally does not exceed 0.3-0.5 m/sec. This makes it possible to precipitate fine particles (average size of the droplets is typically 20-60 microns) and reduce carryover.
Counter-current deposition rate of the particles are smaller and therefore there is more residence time in the chamber. It allows receiving the dried material with a higher density. With countercurrent moving coolant efficiency of the plant is higher and the residual humidity is less, but however co-current flow or combined units are used in producing more often.
Thus drying units spray type allow to obtain a fine powder of the required quality in a relatively short time.
To choose and buy spray dryer - take a consultation of our managers.