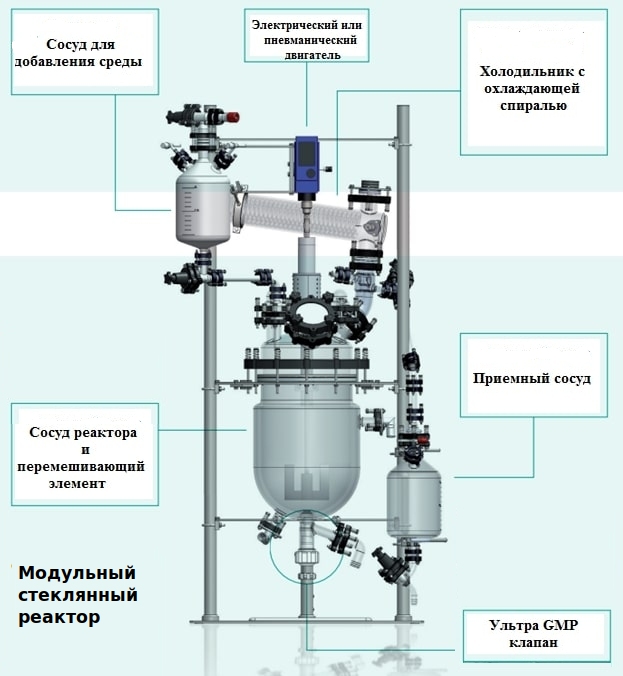
Химические реакторы — это устройства для проведения химических реакций в заданных условиях, с возможностью наблюдения за процессами и управления ими.
Основные разновидности химических реакторов
Существует большое количество различных типов химических реакторов для использования, как в исследовательских лабораториях, так и на производственных предприятиях: химической, фармацевтической, биологической, косметологической и пищевой промышленности.
Различают следующие основные типы химических реакторов:
- По типу конструкции химические реакторы подразделяют на: емкостные, колонные, трубчатые. Названия определяют соответствующие типы емкостей, в которых происходят реакций.
- По фазовому составу реакционной смеси:
-Гомогенные реакторы – для проведения реакций в одну фазу: газовую, жидкостную или твердую;
-Гетерогенные - для реакций, происходящих в несколько фаз, последовательно или одновременно;
- По гидродинамическим параметрам:
-Смешения — такие устройства применяются если синтез вещества требует непрерывного перемешивания во время реакции или при добавлении новых порций реагентов;
-Вытеснения — такие устройства применяются если различные вещества в реакторе не смешиваются, а при постоянном движении вытесняют друг друга.
- По условиям теплообмена:
-Адиабатические ‐ в реакторе отсутствует теплообмен с окружающей средой и тепло химической реакции полностью расходуется на изменение температуры реакционной смеси.
-Изотермические ‐ в реакторе поддерживают постоянную температуру в ходе всего процесса путем отвода или подвода тепла.
-Политропические ‐ температура в реакторе непостоянна, при этом часть тепла может отводиться от реакционной смеси или подводиться к ней.
- По типу течения процесса:
-Периодического действия - все реагенты загружают до начала реакции, а смесь продуктов отводят по окончании процесса.
-Непрерывного действия (проточные) - все стадии процесса − подача реагентов, химическая реакция, вывод готового продукта − осуществляются одновременно, т. е. как бы параллельно друг другу.
Использование разнообразных химических реакторов, позволят проводить реакции различных типов, значительно упрощать и ускорять процесс синтеза веществ, оптимизировать производственные процессы и сокращать себестоимость получаемых продуктов.
Среди всех типов реакционных устройств наибольшее распространение получили емкостные стеклянные химические реакторы, выпускаемые в совершенно различных вариантах исполнения и комплектации. Такую популярность они завоевали благодаря относительно простой и гибкой конструкций, которая легко адаптируются под различные цели и задачи. Например существуют настольные лабораторные стеклянные реакторы с сосудами объемом несколько литров и большие стационарные производственные устройства объемом более 100 л. Оснащение и комплектация стеклянных реакторов может значительно отличается в зависит от назначения и исполняемых задач.
Принципиальная конструкция стеклянных химических реакторов
Наиболее часто используются емкостные стеклянные реакторы смешения − это аппараты с рабочим сосудом из стекла, снабженные перемешивающим устройством (мешалкой) с электроприводом или реже, циркуляционным насосом.
Такие реакторы представляют собой металлическую раму с устанавливаемой на нее стеклянной реакционной емкостью и другими комплектующими, перечень которых зависит от решаемых задач, т. е. фактически конструкция является модульной.
Рабочие реакционные емкости могут иметь различные объемы (от 0,5 л. до 100 л.) и обычно изготавливается из химически устойчивого боросиликатного стекла, и оснащаются нижним сливом и верхней крышкой.
Крышка обычно имеет несколько горловин для установки дополнительного оборудования и приборов, например таких как:
- Измерителей кислотности (PH - метров);
- Термометров;
- Датчиков давления и манометров;
- Вакуумных насосов;
- Пробоотборников;
- Электромеханических смесителей и т.п.
Также через технологически отверстия крышки выполняются различные манипуляции с реакционными составами и введение химических компонентов. К сливному клапану, подключаются принимающие сосуды.
Специальные стеклянные емкости реакторов имеют высокую прочность и стойкость к агрессивным химическим средам и выпускаются с расчетом на работу при высоких или низких температурах( диапазон от -90 до +250°С), высоком и низком давлении.
Теплообмен в таких реакторах осуществляется за счет терморегулирующих устройств (например терморубашек корпусов или термоотводящих змеевиков внутри них), реже путем частичного испарения жидкого компонента реакционной смеси.
При проведение большинства реакций в стеклянных емкостных химических реакторов требуется перемешивание реакционных сред, что осуществляется с помощью мешалок различных типов приводимых в действие электроприводами.
Основные принципы модульной комплектации стеклянных химических реакторов
В современной ситуации стеклянные химические реакторы обычно собирается по модульному принципу под заказ клиентов. Такой подход к построению конструкции позволяет создавать аппараты под определенные цели и задачи с высокой производительностью и эффективностью, обеспечивая наименьшие затраты.
Обычно в базовую комплектацию стеклянного химического реактора входят:
- Опорная рама или штатив из высококачественной нержавеющей стали.
- Реакционный сосуд из боросиликатного стекла, стойкий к воздействию химических реагентов , высокой температуре и давлению.
- Крышка с горловинами под установку дополнительных устройств.
- Лабораторная мешалка (могут быть разных типов).
- Электромотор для вращения мешалки (мощность подбирается под определенные задачи).
- Электронный автоматизированный блок управления.
- Датчики температуры и давления (могут быть разных типов).
- Клапан сброса давления.
- Холодильник.
- Подающая воронка.
- Сливной клапан.
- Крепежные и соединительные элементы.
Для расширения комплекта стеклянных реакторов часто используют следующие элементы:
- Кондесаторы.
- Дозирующие емкости.
- Ручные пробоотборники.
- Распределители потоков.
- Дополнительные адаптеры крепления шлангов.
- Приемные емкости.
- Нагревательные или охлаждающие приборы:
-чиллеры.
- Насосы:
-вакуумные;
-циркуляционные;
-перекачивающие.
Отдельное внимание уделяют подбору системы управления реактором и датчиков необходимых для контроля протекания химических процессов. Это связано с автоматизацией реакторов, которая на данный момент достигла таких высот, что позволяет синхронизировать и объединить процессы снятия параметров с датчиков, с процессом управления. Показания датчиков позволяют получать данные о процессах, происходящих в реакторе а программное обеспечение обрабатывает информацию и отображает картину процесса и управляет процессом.
Особенности модульной комплектации стеклянных химических реакторов.
Наиболее часто, при сборке емкостных стеклянных химических реакторов, специалисты уделяют внимание следующим и элементам:
- Системам регулирования температуры реактора.
- Устройствам для перемешивания реакционной среды.
- Измерительным приборам и датчикам для контроля реакционных процессов.
Основные типы систем теплообмена емкостных стеклянных реакторов
Большое количество химических реакций протекают с выделением тепла и требуют его отвода для регулирования температуры.
Теплообменными поверхностями в реакторах обычно являются наружные стенки, снабженные терморегулирующими рубашками.
Можно выделить два основных типа систем теплоотвода стеклянных реакторов: с одиночными и двойными терморубашками.
Для химических реакции с различными требованиями к температурным режимам необходимо подбирать свой вариант системы терморегулирования.
Если наружных поверхностей реактора недостаточно для теплоотвода, то при относительно низкой вязкости реакционной среды, внутри аппаратов устанавливают дополнительные терморегулирующие поверхности, такие как: змеевики и стаканы. Эти элементы очень эффективны, так как имеют в 2 раза более высокий коэффициент теплоотвода, чем внешние теплообменные системы.
Системы перемешивания реакционной среды, типы мешалок емкостных стеклянных реакторов
В стеклянных химических реакторах перемешивание применяется для равномерного распределения химических веществ и уровня температуры в объеме рабочей емкости.
Различают следующие способы перемешивания:
-Механическое перемешивание — осуществляется как в жидкой среде, так и в материалах различной вязкости с помощью мешалок различного типа.
-Циркуляционное перемешивание — реализуется насосом за счет придания жидкости больших скоростей движения. Такое перемешивание часто применяют для отвода тепла, прокачиванием реакционной среды через теплообменник.
-Барботажное перемешивание - осуществляется с помощью прокачивания газа через жидкость.
Соответственно для обеспечения различных типов перемешивания необходимо применять различные устройства: механические мешалки, циркуляционные гидравлические или пневматические насосы.
Наиболее часто для перемешивания реакционной среды в реакторах используются мешалки разных типов:
- Листовые ( рисунок - а);
Это самые простые мешалки. Могут иметь различную рабочую площадь. Обычно, применяются для перемешивания жидкостей с низкой вязкостью.
- Лопастные (рисунок - б);
Применяются при перемешивании жидких неоднородных систем с вязкостью до 15 Па⋅с и с плотностью до 2000 кг/м. куб.
- Якорные (рисунок - д);
Предназначены для перемешивания жидкостей с вязкостью 300 Па⋅с и выше в реакторах, где нагревание среды происходит через терморубашку. Для повышения эффективности работы могут снабжаться дополнительными вертикальными элементами.
- Рамные (рисунок - е);
- Применяются при перемешивании значительных объемов вязких материалов в реакторах с большой емкостью.
- Турбинные (рисунок - в);
Работают по принципу центробежного насоса, всасывая жидкость в середину и отбрасывая ее к периферии за счет центробежной силы. Турбинные мешалки обеспечивают интенсивное перемешивание жидкостей вязкостью до 450 Па⋅с и плотностью до 2000 кг/м. куб.
- Пропеллерные (рисунок - г);
Представляют собой аналог гребного винта с 2 — 4 лопастями. Используются для перемешивания сред вязкостью до 2 Па⋅с и плотностью до 2000 кг/м. куб.
- Специальные (рисунки ж-з).
Это ленточные и шнековые мешалки которые — используются для перемешивания очень вязких жидкостей и пастообразных материалов. Их преимуществом является способность, очищать стенки емкости реакторов от налипающей реакционной массы.
В зависимости от числа оборотов мешалки условно делят на:
-тихоходные - 80−100 об/мин., это лопастные, рамные, якорные и листовые.
-быстроходным – более 100 об/мин., это турбинные и пропеллерные.
Основные измерительные приборы и датчики емкостных стеклянных реакторов
Измерительные приборы и датчики в химических реакторах необходимы для получения данных о протекании реакций, а также для осуществления контроля и управления процессом.
Среди основных измерительных приборов и датчиков можно выделить следующие:
Манометры - это приборы, измеряющие давление жидкости или газа в замкнутом пространстве, в классическом варианте действие таких приборов основано на уравновешивании измеряемого давления силой упругой деформации трубчатой пружины, один конец которой запаян в держатель, а другой через тягу связан с трибко-секторным механизмом, преобразующим перемещение упругого элемента в круговое движение стрелки.
Датчики давления - устройства, физические параметры которых изменяются в зависимости от давления измеряемой среды (жидкости, газа, пара). В современных датчиках параметры давления измеряемой среды преобразуется в электрические сигналы или цифровой код, при этом они могут быть реализованы на разных физических принципах: тензеометрическом, пьезорезистивном, емкостном, резонансном, индуктивном, пьезоэлектрическом.
Вакууометры - это вакуумные манометры предназначенные для измерения давления разряженных газов. Существуют, как классические вакууметры работающие на принципах подобных, но обратных тем, что используются в манометрах, так и различные современные электронные вариации данных устройств построенные на разных физических принципах: емкостном, терморезистивном, термопарном, ионизационном.
Датчики температуры - это устройства, непосредственно принимающее измеряемую температурную величину и преобразующие ее в электрический или цифровой сигнал для последующей передачи его на контрольные приборы или системы управления. Датчики температуры бывают следующих видов: термопары; интегральные; биметаллические; диодные; термисторы; пирометры; кремниевые.
Так же могут использоваться и другие датчики:
Датчики кислотности жидкости (pH-метр) - это датчики, позволяющий определить pH (potentia Hydrogenii) уровень жидкостей. Учистой воды (H2O) при температуре 25 °C нейтральный уровень pH = 7. Чем выше кислотность жидкости, тем ниже её уровень pH, а в щелочных растворах уровень pH выше.
Датчик мутности — это встраиваемый аналитический прибор, предназначенный для непрерывного измерения концентрации взвешенных частиц в различных технологических процессах. Оптический сенсор датчика мутности обеспечивает широкий диапазон измерений наличия взвешеных частиц в мг на литр жидкости.
Датчик размеров частиц - позволяет определять распределение частиц по размерам непосредственно в реакторе. Такие датчик предназначен для работы с широким диапазоном размеров частиц. Их работа основана на технологии отражения света лазера, обеспечивающей динамические (онлайн) измерения распределения размеров частиц.
Датчики подбирается под типы проводимых реакций, а также в соответствии с целями и задачами стоящими перед заказчиками.
Набор датчиков, компьютерная система управления и специальное ПО позволяют собирать данные о течении химического процесса и управлять им в автоматическом режиме.
Автоматическая система управления реактором обычно имеет удобное ПО, интуитивно понятное с визуализацией данных и многочисленными уникальными возможностями, такими как: графическое отображение данных в реальном времени; возможность управления реакцией в ходе эксперимента; аварийную сигнализацию и отключение при возникновении критических параметров; возможность импорта и экспорта данных для обработки.
Основные аксессуары и комплектующие для модульной комплектации стеклянных реакторов
Возможность сборки стеклянных реакторов по модульной схеме является идеальным решением для научно исследовательских лабораторий, поскольку, по доступной цене, из различных комплектующих можно собрать специализированную систему под сложные цели и задачи. Имеется возможность комплектовать установки всеми необходимыми элементами оборудования и в последствии заменять их по необходимости.
Ниже на фото можно увидеть наиболее часто применяемое на стеклянных реакторах оборудование и аксессуары:
- Перемешивающие элементы
- Холодильники
- Капельные воронки
- Вакуумметры и манометры
- Погружные трубки
- Термометры
- Приёмные колбы
- Переходники
- Коннекторы для шлангов
Процесс сборки реактора можно посмотреть на демовидео
Стеклянные реакторы от компании "Мида"
Наша компания осуществляет поставки стеклянных реакторов в различных комплектациях под заказ клиентов. Специалисты компании «Мида» помогут подобрать необходимый вариант оборудования под ваши задачи, организуют поставку, установку, гарантийное и послегарантийное обслуживание.
Получить дополнительную информацию и сделать заказ можно, обратившись за консультацией по телефону +7 (495) 145-06-01 или электронной почте info@mida.ru.
Перейти в раздел каталога
Реакторы стеклянные